How to control the biggest cost-drivers of robotic automation

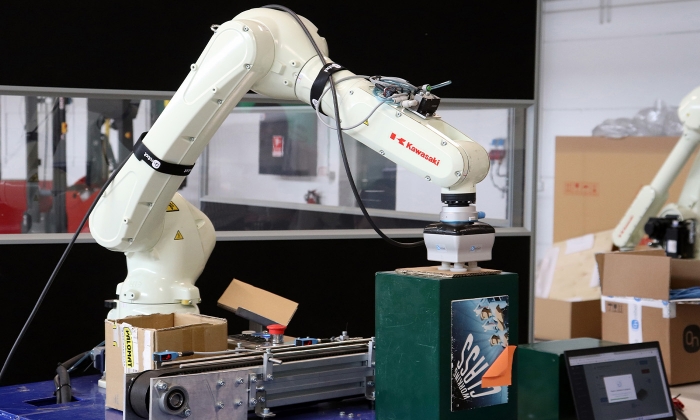
Are you holding off on robotic automation because the cost is too high and the return on investment too far off in the future? This article will demonstrate why the no-code deployment platform D:PLOY is the secret weapon that will enable you to take control of the primary cost drivers and reap the benefits of robotic automation ahead of the competition.
You know you need an edge to stay competitive as an SME manufacturer. And you know robotic automation could give you that edge. The question is: Will robotic automation give you a fast enough and big enough return on investment to make it cost-effective?
Your competitors are being held back by similar concerns. According to this 2022 report by McKinsey, securing return on investment is a major bottleneck for robotic automation across industrial sectors.
But OnRobot’s no-code integration platform, D:PLOY, has turned the tables on robotic implementation, which is why now is the time for the intelligent SME manufacturer to strike. With D:PLOY, you can control the three biggest cost drivers of robotic automation: hardware, deployment time and training, and get a head start on cost-effective factory automation. Read further to discover how.
How to control the biggest automation cost-drivers with D:PLOY
Cost driver #1: Robotic hardware
The upfront capital expenditure on robotic equipment often represents a substantial portion of the overall expenses, and as there is no standard programming language in robotics, you must confine yourself to one robot brand for all your hardware needs or pay professional programmers a king’s ransom for system integration.
Free choice of robotic hardware brings down initial cost
While D:PLOY cannot help you negotiate a better price on your robotic hardware, the platform seamlessly integrates end effectors with a wide range of robot brands.
This means you are free to choose the robotic hardware that best suits your application and budget, regardless of brand and programming language.
Cost driver #2: Deployment
Deploying your robotic applications is another critical cost driver in robotic factory automation. The complexity of integrating disparate automation components and ensuring seamless communication and coordination among different systems can require substantial investments in engineering and system integration services. Not to mention the weeks or months you must wait for the robotic application to be up and running, earning its keep.
Up to 90 % reduction in time spent on deployment
Faster deployment of your robotic applications means fewer system integration costs and faster ROI. Our tests show that D:PLOY reduces the deployment time of a robotic application by up to 90 % compared to conventional programming.
The amount of time saved on deployment depends on the specific application:
Deploying a Palletizing application with D:PLOY:
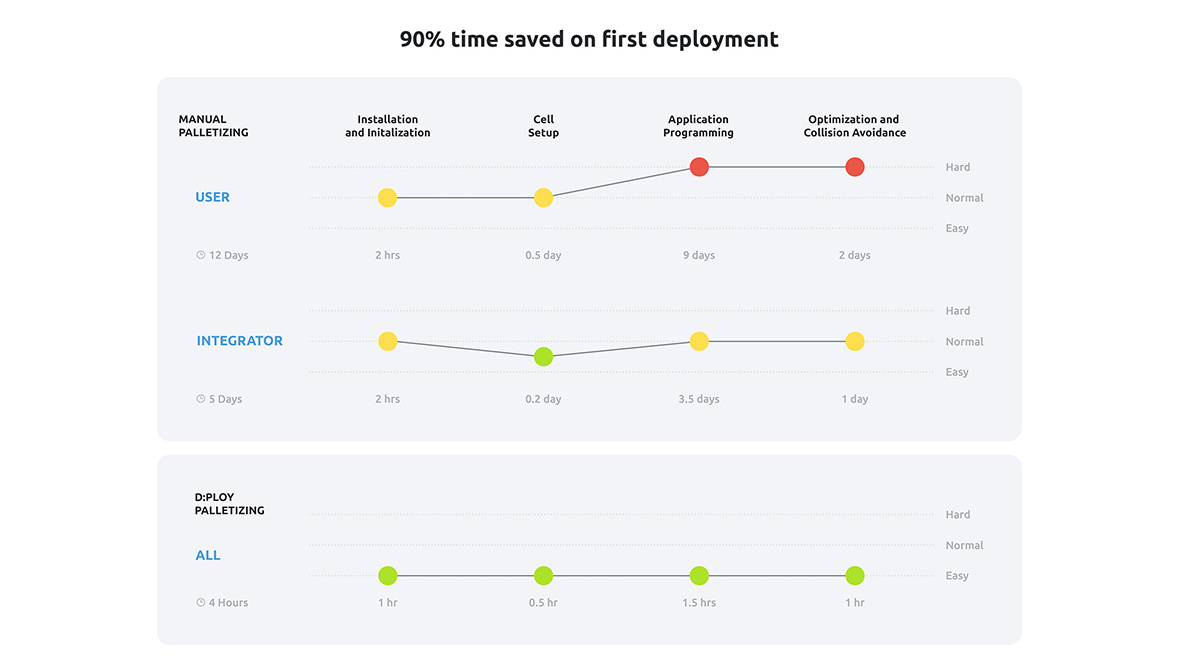
Deploying a packaging application with D:PLOY:
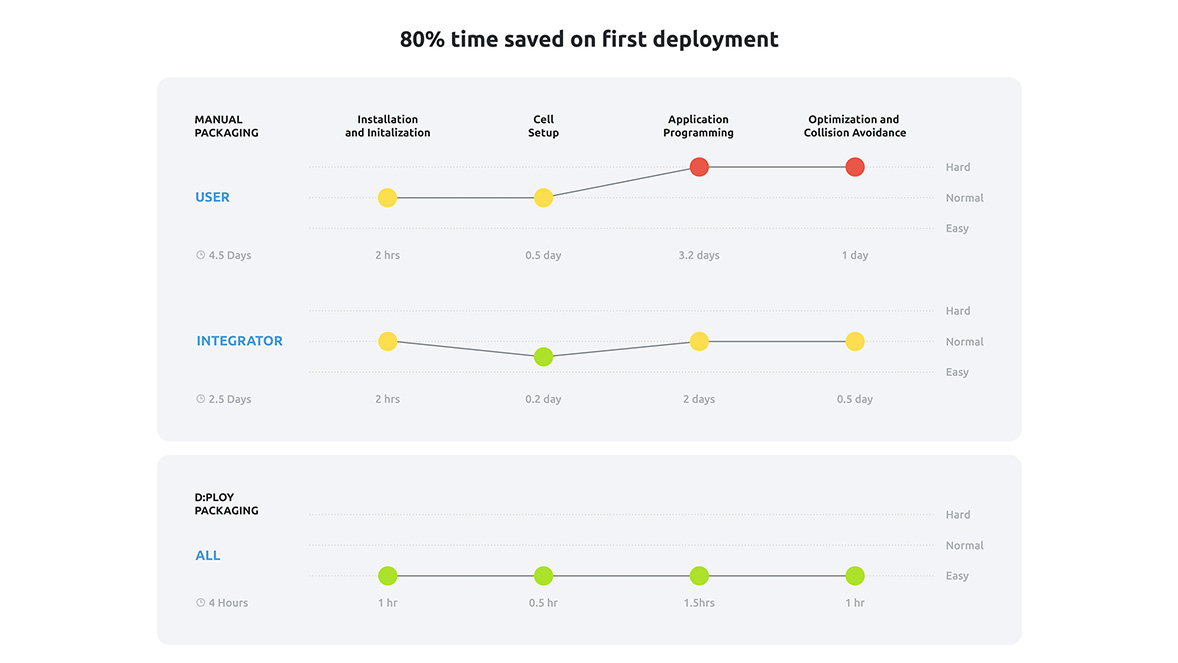
Deploying a CNC machine tending application with D:PLOY:
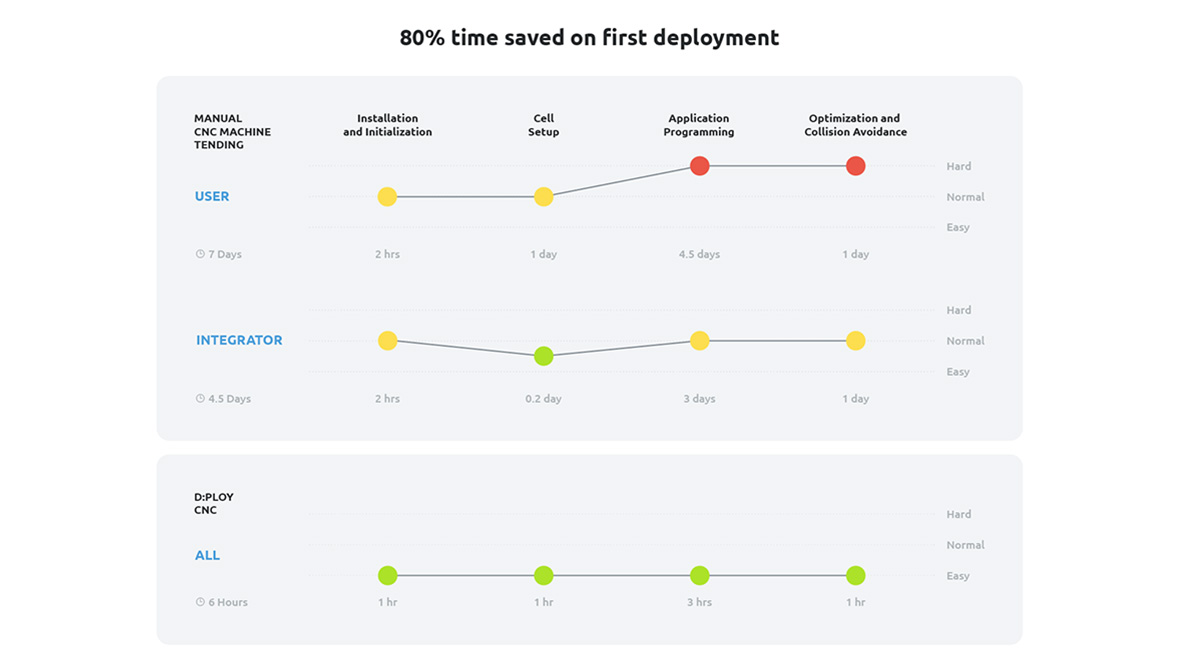
Cost-driver #3: Workforce training and upskilling
Low-volume, high-mix production requires frequent adjustments and redeployments of robotic applications, so to cost-effectively automate your production line, you need to have the skills to effectively operate and maintain the complex robotic applications in-house.
However, training and upskilling a low-skilled work force can be a significant cost driver if you are relying on conventional programming. Investments in training programs, retraining initiatives, and attracting skilled personnel can contribute significantly to overall expenses.
How D:PLOY eliminates the programming barrier
D:PLOY automatically handles most of the system integration and programming. The no-code platform has an intuitive, app-like interface which allows workers with no programming experience to successfully deploy and redeploy a robotic application in less time than it takes a professional system integrator to deploy the application with conventional programming. And if you prefer the expertise of the professionals, they, too, can deploy much faster with D:PLOY.
Our tests show that you save up to 91 % of the time spent on redeployments when using D:PLOY – with or without programming experience – compared to conventional programming. The amount of time saved depends on the application:
Redeploying a palletizing application with D:PLOY vs. conventional programming:
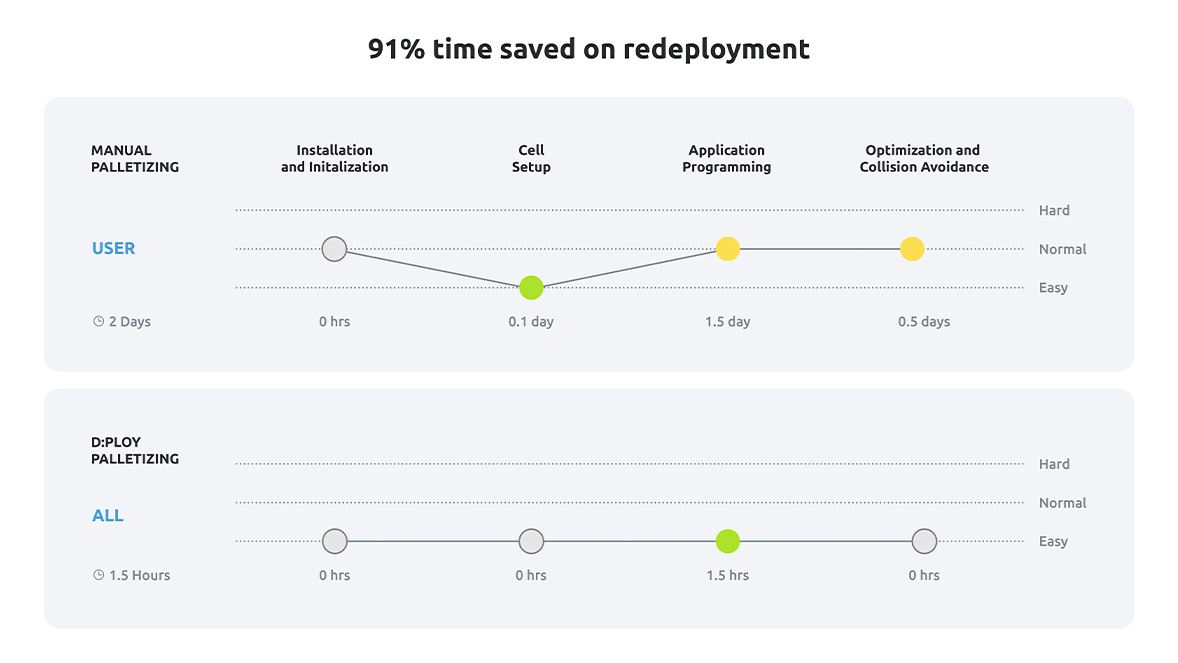
Redeploying a packaging application with D:PLOY vs. conventional programming:
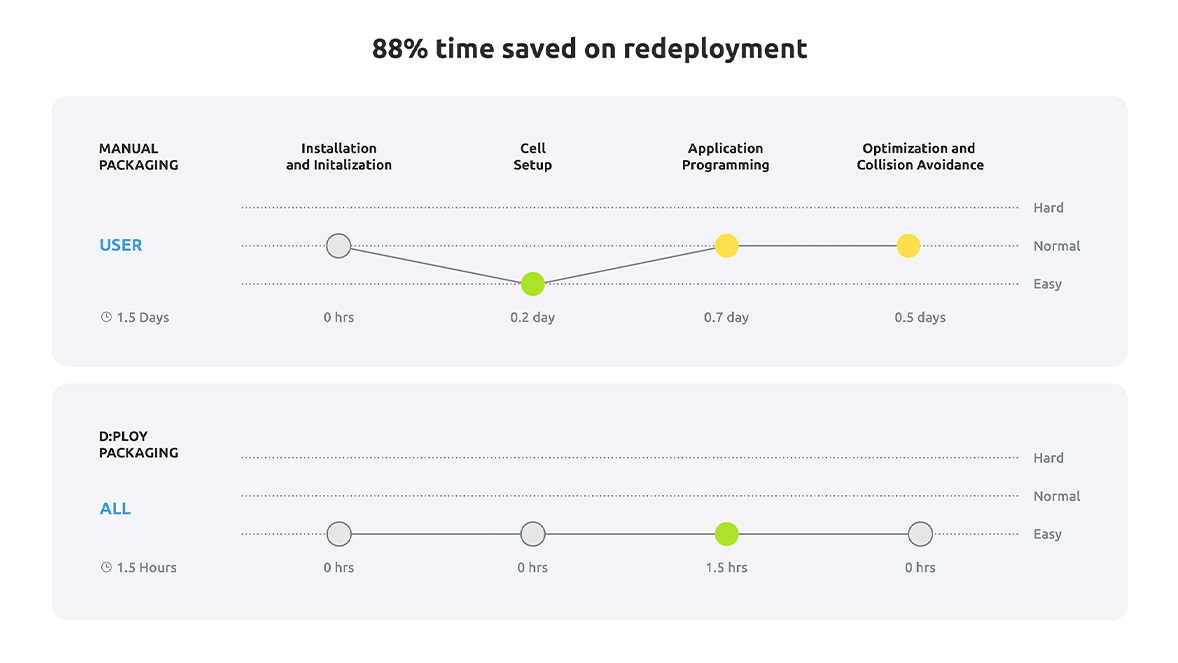
Redeploying a CNC machine tending application with D:PLOY vs. conventional programming:
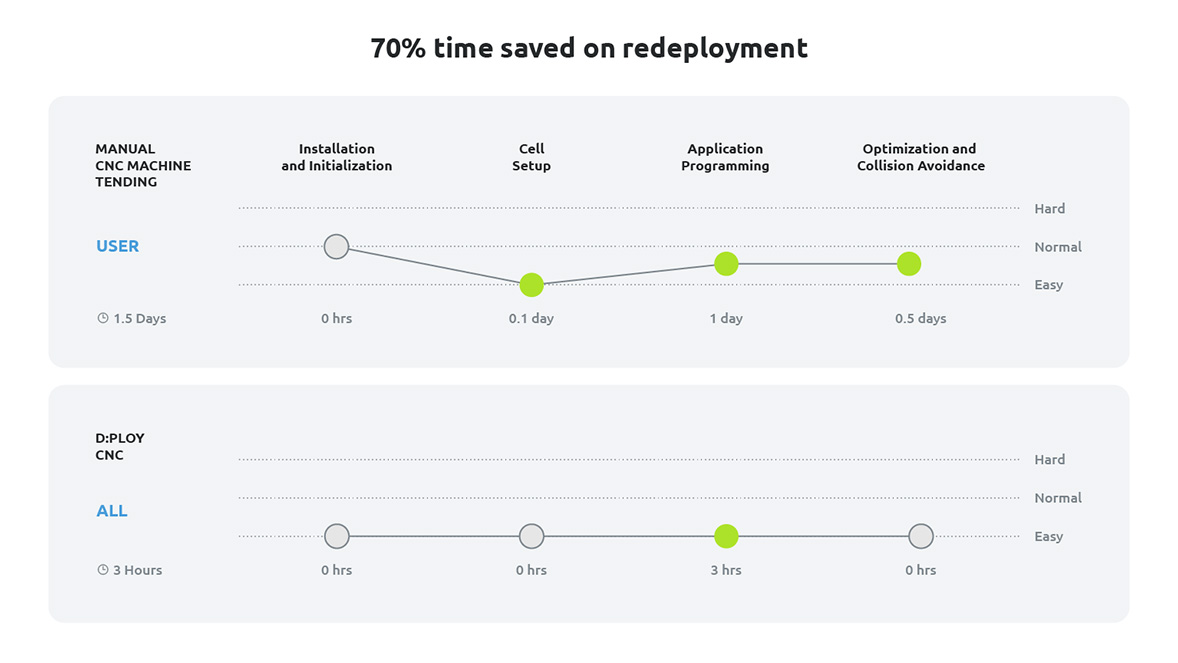
As demonstrated, D:PLOY enhances your control of the three biggest cost-drivers in robotic factory automation: robotic hardware, deployment and training, by:
- giving you the freedom to choose the hardware best suited to your needs and budget, regardless of brand
- reducing the deployment and redeployment time by up to 91 %
- lowering the programming bar to allow workers with no programming experience and minimal training to deploy and redeploy robotic applications in a matter of hours.
In short, deploying and redeploying robotic applications has never been faster, nor more cost-effective. You know it. Your competitors will soon know of it, too.
So why are you still here?
Get that head start on automation with D:PLOY today!
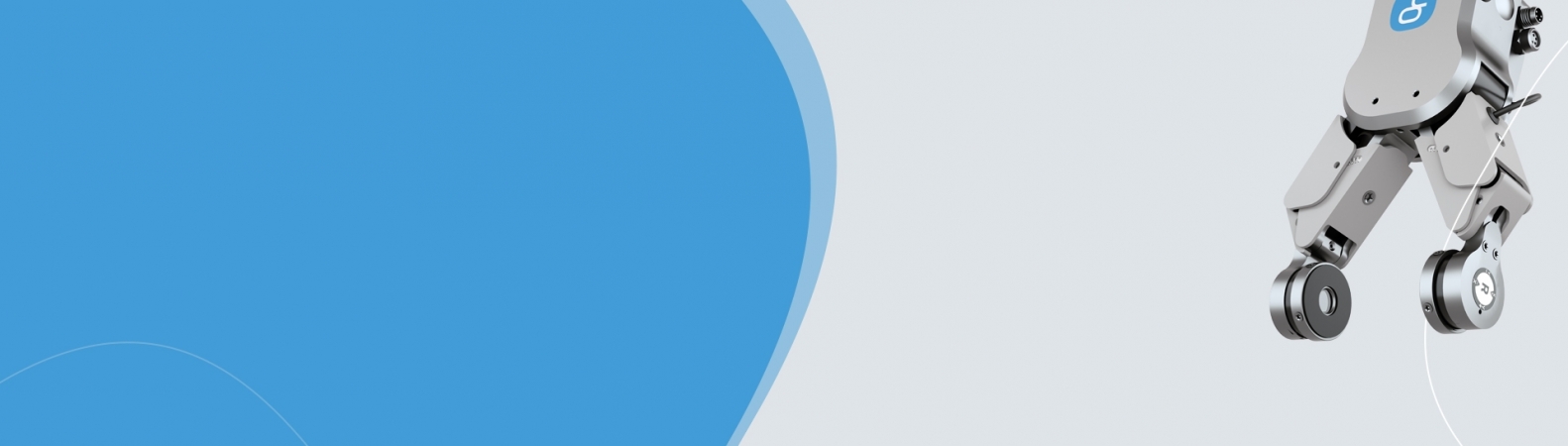
Jak rozvíjet podnikání pomocí kolaborativních aplikací
Díky rozkvětu chytřejších a přizpůsobivějších nástrojů mohou roboty nyní fungovat rychleji, přesněji a s větší silou, plnit celou řadu úkolů a zároveň maximalizovat návratnost investic. V naší elektronické brožuře získáte další informace o tom, jak zrychlit produkci při nižších nákladech.
ZÍSKAT BEZPLATNOU ELEKTRONICKOU BROŽURU
|
![]() |
